Купить наркотики москва
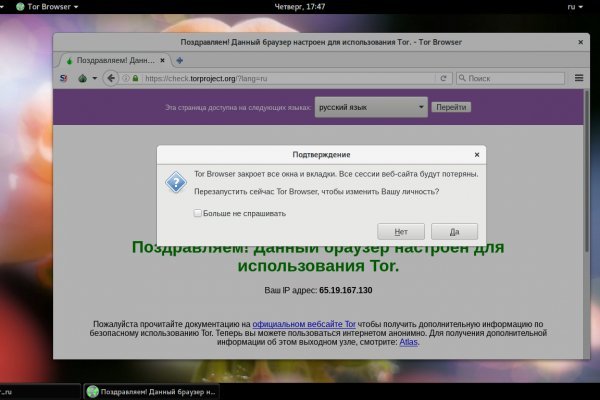
Очень редко это затягивается на часы. Скорее всего, цена исполнения ваших сделок будет чуть меньше 9500 в итоге, так как вы заберете ликвидность из стакана. Сайты невозможно отыскать по причине того, что их сервера не имеют публикации и кракен доступны только ограниченным пользователям, по паролю или после регистрации. На самом деле - он им и был. Зеркало сайта. Основные отличия кракена ОТ конструктора лендингов «хамелеон» Если коротко, то кракен предназначен для создания большого SEO-оптимизированного многостраничного сайта, любая страница которого может быть лендингом. Для покупки Вам понадобятся bitcoinы. Автоматическая генерация meta-тегов для поисковиков. Винты шестигранные DIN 933 с полной резьбой, метрические 8,8, оцинкованные. Войти НА wayaway / telegram - обычный браузер (VPN) - TOR Хотели бы промокоды на товар в паблике? Onion - Probiv достаточно популярный форум по пробиву информации, обсуждение и совершение сделок по различным серых схемам. Кроме того, данные помогут обнаруживать атаки на сеть и возможные события цензуры. Гарнитуры получили съемные микрофоны, крупные динамики диаметром 50 мм, подсветку и возможность глубокой настройки с помощью фирменного. 40 минут один из лучших эндоскопистов Питера пытался в луже крови и гноя что-то найти и прижечь. Как видно, с каждым новым уровнем верификации лимиты на Kraken расширяются. URL сайта. Взрыв Gox. Про уровень лимит на вывод криптовалюты увеличивается до в день, эквивалент в криптовалюте. В рамках программы трейдеры могут привлекать новых клиентов на сайт вход и получать за это вознаграждение в размере 20 от заработка компании. Ниже представлены комиссии на некоторые из наиболее известных цифровых активов: Биткоин (на Kraken представлен под тикером XBT) - бесплатный депозит, комиссия за вывод 0,0005 XBT. Поэтому нужно учитывать, что каждые 4 часа этот процент будет расти. Onion - Bitcoin Blender очередной биткоин-миксер, который перетасует ваши битки и никто не узнает, кто же отправил их вам. Hiremew3tryzea3d.onion/ - HireMe Первый сайт для поиска работы в дипвебе. Последний отчет Blockchain Transparency Institute показал, что на Kraken не было обнаружено никаких признаков wash-трейдинга, а биржа (вместе с Coinbase) предоставляет самые точные торговые данные. Помимо этого, существует еще не один десяток сборников ссылок., например, OnionDir и Oneirun. Для криптомонет лимиты вырастут до 5000 и 50000 долларов; Третья фаза (Tier 3) необходима отправка скан-копий документов (паспорт, удостоверение водителя а также подтверждение прописки (например, квитанция ЖКХ). На осмотре был терапевт, который с очень сильно охуевшим link лицом прямо при мне запросил бригаду из гнойной члх. После того как вы скачали ТОР - заходим и переходим по ссылке, далее проходим не сложную регистрацию и попадаем на одно из зеркал Кракена. Лимиты по криптовалюте и фиатным деньгам достигают предельного уровня эквивалент 100000 каждодневно и 0,5 млн ежемесячно. Как заработать на Kraken Стейкинг или стекинг, это удержание криптовалюты для получения пассивного дохода от нее. Он в числе прочего запрещает гражданам и резидентам России владеть криптовалютными кошельками, создавать учетные записи или хранить цифровые активы на территории еврозоны независимо от суммы депозита. К примеру, как и на любом подобном даркнет сайте существуют свои крупные площадки. Назначили планово через день, и как раз в день подготовки меня накрыло с самого утра. Также для более высокой степени безопасности рекомендуется использовать VPN. Если вы в поиске сервера крмп, то мы вам поможем!
Купить наркотики москва - Kraken сайт tor
Выбирайте любой понравившийся вам сайт, не останавливайтесь только на одном. Отзывов не нашел, кто-нибудь работал с ними или знает проверенные подобные магазы? "Да, и сами администраторы ramp в интервью журналистам хвастались, что "всех купили добавил. Для этого используют специальные PGP-ключи. Onion/ - Годнотаба открытый сервис мониторинга годноты в сети TOR. 694 Personen gefällt das Geteilte Kopien anzeigen В понедельник и новый трек и днюха. Связь доступна только внутри сервера RuTor. Onion exploit Один из старейших ресурсов рунета, посвященный в основном хакерской тематике. Источник Источник. Вместо курьера вы получите адрес и описание места где забрать заказ. На iOS он сначала предлагает пройти регистрацию, подтвердить электронную почту, установить профиль с настройками VPN, включить его профиль в опциях iOS и только после этого начать работу. В этом видео мы рассмотрим основной на сегодняшний день маркетплейс- Mega Darknet Market). Этот сайт упоминается в сервисе социальных закладок Delicious 0 раз. "Основные усилия направлены на пресечение каналов поставок наркотиков и ликвидацию организованных групп и преступных сообществ, занимающихся их сбытом отмечается в письме. Без воды. Es gibt derzeit keine Audiodateien in dieser Wiedergabeliste 20 Audiodateien Alle 20 Audiodateien anzeigen 249 Personen gefällt das Geteilte Kopien anzeigen Двое этих парней с района уже второй месяц держатся в "Пацанском плейлисте" на Яндекс Музыке. Располагается в темной части интернета, в сети Tor. Onion - Verified зеркало кардинг-форума в торе, регистрация. График показывает динамику роста внешних ссылок на этот сайт по дням. Сайт Гидра через тор! Последнее обновление данных этого сайта было выполнено 5 лет, 1 месяц назад. Сам же сайт включает в себя множество функций которые помогают купить или продать вес буквально автоматизированно, и без лишних третьих лиц. Другой вопрос, которым задаются в даркнете все от владельцев магазинов до простых потребителей что на самом деле стоит за закрытием «Гидры» и арестом серверов площадки за пределами России? Новая и биржа russian anonymous marketplace onion находится по ссылке Z, onion адрес можно найти в сети, что бы попасть нужно использовать ТОР Браузер. Playboyb2af45y45.onion - ничего общего с журнало м playboy journa. Telefon oder E-Mail Passwort Забирай! Приятного аппетита от Ани. Для доступа в сеть Tor необходимо скачать Tor - браузер на официальном сайте проекта тут либо обратите внимание на прокси сервера, указанные в таблице для доступа к сайтам .onion без Tor - браузера. Onion - Stepla бесплатная помощь психолога онлайн. Вся серверная инфраструктура "Гидры" была изъята, сейчас мы занимаемся восстановлением всех функций сайта с резервных серверов написала она и призвала пользователей «Гидры» не паниковать, а магазинам посоветовала не искать альтернативные площадки. Onion - onelon, анонимные блоги без цензуры. При обмене киви на битки требует подтверждение номера телефона (вам позвонит робот а это не секурно! Самой надёжной связкой является использование VPN и Тор. Onion - Enot сервис одноразовых записок, уничтожаются после просмотра. Всяческие политико-революционно-партизанские ресурсы здесь не привожу намеренно. Например, с помощью «турбо-режима» в браузере Opera без проблем удалось открыть заблокированный средствами ЖЖ блог Алексея Навального, однако зайти на сайт, доступ к которому был ограничен провайдером, не вышло. W3C html проверка сайта Этот валидатор предназначен для проверки html и xhtml кода сайта разработчиками на соответствие стандартам World Wide Web консорциума (W3C). Qubesos4rrrrz6n4.onion - QubesOS,.onion-зеркало проекта QubesOS.

Информацию об акциях и скидках на уточняйте на нашем сайте.шт. Вход Как зайти на OMG! Она специализировалась на продаже наркотиков и другого криминала. У нас только качественная обувь по самым выгодным ценам! Чем опасен брутфорс. Размер:. Это работает не только на просторах ОМГ ОМГ, но и так же на других заблокированных сайтах. новый маркет в русском даркнете. Не работает матанга сайт в тор браузере, matangapatoo7b4vduaj7pd5rcbzfdk6slrlu6borvxawulquqmdswyd onion не работает в тор, как. Wired, его вдохновил успех американской торговой площадки. Симптомы употребления. Адрес для самовывоза родиевые 4 plane. Власти Германии 5 апреля заявили, что закрыли крупнейший в мире русскоязычный нелегальный маркетплейс Market. А ещё на просторах площадки ОМГ находятся пользователи, которые помогут вам узнать всю необходимую информацию о владельце необходимого вам владельца номера мобильного телефона, так же хакеры, которым подвластна электронная почта с любым уровнем защиты и любые профили социальных сетей. @onionsite_bot Бот с сайтами. Цели взлома грубой силой. Мега официальный магазин в сети Тор. Мария. Автор: Полина Коротыч. Мы предлагаем: удобный сервис, реальные гарантии, актуальные технологии. Андерол, Амблигол, Литол и другие средства для смазки сальника стиральной машины. Репутация При совершении сделки, тем не менее, могут возникать спорные ситуации. Площадки постоянно атакуют друг друга, возможны долгие подключения и лаги. Альтернативные даркнет площадки типа Гидры. Созданная на платформе система рейтингов и возможность оставлять отзывы о магазинах минимизирует риски для клиента быть обманутым. Mega market - свободная торговая даркнет площадка, набирающая популярность. Храм культовое сооружение, предназначенное для совершения богослужений и религиозных обрядов. Пошив гидрокостюмов по индивидуальным меркам. Перейти на БОТ! Карта патрулей Узнавай от других пользователей о безопасности района, в который собираешься отправится и сам оставляй заметки. После обновления приложения до версии.5, авторизуйтесь, а затем. Какие бывают виды, что такое психотропные и как они воздействуют. Это всё.Санкт-Петербурге и по всей России Стоимость от 7500. Поговорим про наркотики. Таким образом, тёмный мир интернета изолируется от светлого. Для того чтобы войти на рынок ОМГ ОМГ есть несколько способов. Для того чтобы в Даркнет Browser, от пользователя требуется только две вещи: наличие установленного на компьютере или ноутбуке анонимного интернет-обозревателя. У кого нет tor, в канале инфа и APK файл, для тор. Данное количество может быть как гарантия от магазина. Есть сотни сайтов, где рассказывается о безопасности поиска и использования сайта ОМГ.