Кракен наркомаркет
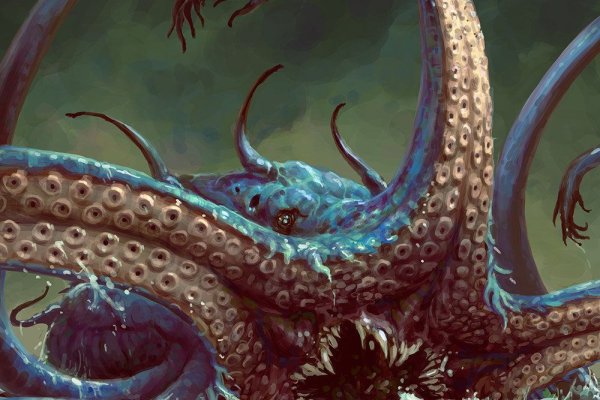
Число устройств, с которых можно использовать VPN одновременно. Дополнительная безопасность. Можно подключить пять устройств с одного аккаунта, строгая политика отсутствия журналов, можно получить VPN с частным DNS. Если существует необходимость лишь периодически заходить на заблокированные сайты, тогда лучше воспользоваться ВПН. Они расположены по всему миру, а трафик перенаправляется на эти серверы, скрывая реальный IP-адрес пользователя. 485333 Драйвера и ПО к USB-эндоскопу ViewPlayCap. Блокировка доступа к определенным сайтам достаточно распространенная практика. Если указать сервер рядом со своей страной, можно увеличить скорость работы. Использование ВПН самый надежный способ получить доступ к заблокированному сайту. Вскоре ее могут прикрыть (или нет но пока работает. Тогда можно использовать прокси-сервер. Mozilla Firefox В браузере Mozilla, как и в Chrome, есть собственный интернет-магазин с несколькими расширениями для маскировки реального местоположения пользователя. На момент написания статьи доступно 44 расширения. Хорошо, если в сервисе есть выбор протоколов безопасности, таких как OpenVPN, WireGuard, L2TP, pptp и других. Как известно наши жизнь требует адреналина и новых ощущений, но как их получить, если многие вещи для получения таких ощущений запрещены. Поддерживает протоколы безопасности https и socks. Это сервис с разветвленной сетью серверов по всему миру, есть бесплатный пробный период и платная версия с богатым выбором серверов, а установка займет минимум времени и не потребует от пользователя специальных навыков. Rar 289833 Данная тема заблокирована по претензии (жалобе) от третих лиц хостинг провайдеру. Это обобщенное название технологий, которые создают отдельное сетевое соединение поверх другой сети. Но не очень удобные для каждодневного использования, поскольку интернет становится немного медленней. Но в отличие от провайдера, сайт видит ваши действия например, поисковые запросы или зайти заполнение формы. Типов прокси намного больше, но для обхода блокировок сайтов достаточно этих. Или выбрать сервер, на котором работают нужные сервисы. Поэтому стоят денег или предлагают бесплатный тариф с ограничениями для того, чтобы пользователь смог оценить преимущества сервиса. Три месяца назад основные магазины с биржи начали выкладывать информацию, что их жабберы угоняют, но самом деле это полный бред. У него есть серверы по всему миру, предусмотрен бесплатный и платный доступ к Сети и максимально простой интерфейс, чтобы справиться с подключением могли даже новички. Искажающий. Может представлять любой тип прокси выше, но использовать его будет только один пользователь. В Айфонах разблокировка сайта осуществляется через настройки. При этом крайне важно выбирать проверенные продукты, которые реально будут скрывать IP-адрес пользователя, а не фиксировать его личные данные. Опубликуйте заказ на Workspace, проведите конкурс и выберите лучшее предложение с реальными ценами и сроками. Платные и престижные делают это по минимуму и используют данные исключительно в технических целях для улучшения работы сервиса. Все это поможет выбрать удобный тариф и использовать сервис всей семьей или офисом. В браузере Mozilla тоже есть расширения для маскировки реального местоположения пользователя. Не позволяет обнаружить исходный IP-адрес и его самого в качестве прокси. Выполните: Включите перевод с английского на русский. Чтобы обойти блокировку сайта без VPN, откройте «Яндекс. Более 50 млн IP-адресов по всему миру. События рейтинга Были на сайте Новые пользователи mordor PyotrErik DikstraFore long сычев Jack-me-google s Лидеры месяца Current monthноября Not available Мы в Сетке. Не хотите тратиться выбирайте платные сервисы с бесплатным тарифом. По сути, это специальная программа или приложение, которое устанавливают на смартфон или встраивают в браузер. Любой сервис VPN требует затрат на «железо технические расходы и хотя бы одного сотрудника, который будет за всем следить. Ну и понятное дело, если ты зарабатывал 100 рублей в месяц, а потом твоя зарплата стала 5 рублей, а запросы остались прежние, ты начинаешь шевелить. Есть информация о серверах. Но все может быть гораздо хуже. В зависимости от личных предпочтений, можно установить бесплатный или платный VPN, но важно обращать внимание не столько на стоимость, сколько на количество и географическое расположение серверов. Например, это бесит путешественников, которые не могут получить доступ к контенту и соцсетям в родной стране (пока находятся в путешествии или тех, кто работает удаленно, оказывает услуги заказчикам из разных стран и не может использовать привычные сервисы, например, Trello.
Кракен наркомаркет - Кракен браузер
Только сегодня узнала что их закрылся. Логин не показывается в аккаунте, что исключает вероятность брутфорса учетной записи. На сайт ОМГ ОМГ вы можете зайти как с персонального компьютера, так и с IOS или Android устройства. Tor не создает временные файлы, новые записи в реестр. Можно утверждать сайт надежный и безопасный. Ч Архив имиджборд. Клиент, использующий форум не упускает прекрасную возможность быть в самом центре событий теневого рынка Мега. Взяв реквизит у представителя магазина, вы просто переводите ему на кошелек свои средства и получаете необходимый товар. Минфин США ввело против него санкции. Хотя слова «скорость» и «бросается» здесь явно неуместны. Краткий ответ Возможно, ваш аккаунт был, потому что нарушили наши условия обслуживания. С какой-то стороны работа этих сайтов несет и положительную концепцию. Возможность оплаты через биткоин или терминал. Onion - Нарния клуб репрессированных на рампе юзеров. Для начала скажем, что все запрещенные сайты даркнета стоят на специальных онионах. Всяческие политико-революционно-партизанские ресурсы здесь не привожу намеренно. Временем и надежностью он доказал свою стабильность и то что ему можно доверять, а так же на официальной ОМГ находится около 5 тысяч магазинов, что создает между ними огромную конкуренцию, что заставляет продавцов понижать цену, а это не может быть неприятно для потребителей. Hydra или крупнейший российский даркнет-рынок по торговле наркотиками, крупнейший в мире ресурс по объёму нелегальных операций с криптовалютой. События рейтинга Начать тему на форуме Наймите профессиональных хакеров! Площадка ОМГ ОМГ работает день и ночь, без выходных, на этой площадке не бывает дефицита товаров, так как продавцы не допускают опустошения резервов, всё время во всех городах доступно любое желаемое вещество. Таких людей никто не любит, руки бы им пообломать. Onion - PIC2TOR, хостинг картинок. Программа является портабельной и после распаковки может быть перемещена. Отключив серверы маркета, немецкие силовики также изъяли и крупную сумму в криптовалюте. Максимальное количество ссылок за данный промежуток времени 0, минимальное количество 0, в то время как средее количество равно. Playboyb2af45y45.onion - ничего общего с журнало м playboy journa. Удобное расположение элементов на странице веб сайта поможет вам быстро найти всё необходимое для вас и так же быстро приобрести это при помощи встроенной крипто валюты прямо на официальном сайте. Крупнейшая онлайн-площадка по продаже наркотиков прекратила свою. Для Android есть его аналог под названием Orweb. Просто покидали народ в очередной раз, кстати такая тенденция длилась больше 3 лет. Как зарегистрироваться на Mega?
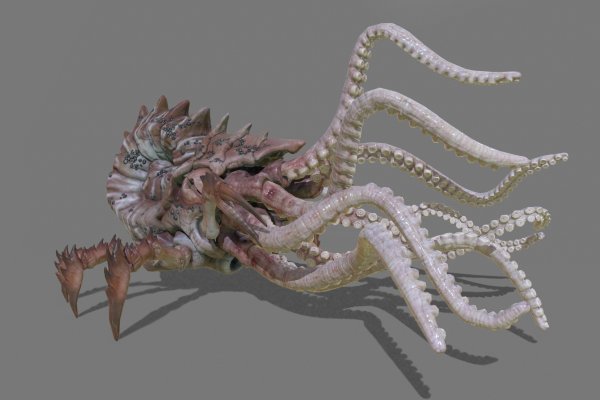
Whisper4ljgxh43p.onion - Whispernote Одноразовые записки с шифрованием, есть возможность прицепить картинки, ставить пароль и количество вскрытий записки. Жека 3 дня назад Работает! Что такое брутфорс и какой он бывает. Стоит помнить внешний вид Мега Шопа, чтобы не попасть на фейки. Окончательно портит общее впечатление команда сайта, которая пишет объявления всеми цветами радуги, что Вы кстати можете прекрасно заметить по скриншоту шапки сайта в начале материала. Есть закрытые площадки типа russian anonymous marketplace, но на данный момент ramp russian anonymous marketplace уже более 3 месяцев не доступна из за ддос атак. Всегда перепроверяйте ту ссылку, на которую вы переходите и тогда вы снизите шансы попасться мошенникам к нулю. Старая. Воспользуйтесь специальной строкой для поиска по онион сети. Список ссылок обновляется раз в 24 часа. Onion - ProtonMail достаточно известный и секурный имейл-сервис, требует JavaScript, к сожалению ozon3kdtlr6gtzjn. Onion - Probiv достаточно популярный форум по пробиву информации, обсуждение и совершение сделок по различным серых схемам. Вскоре представитель «Гидры» добавил подробностей: «Работа ресурса будет восстановлена, несмотря ни на что. Epic Browser он с легкостью поможет Вам обойти блокировку. Information премьера Adam Maniac Remix Премьера сингла! Витя Матанга - Забирай Слушать / Скачать: /ciB2Te Es gibt derzeit keine Audiodateien in dieser Wiedergabeliste 20,353 Mal abgespielt 1253 Personen gefällt das Geteilte Kopien anzeigen Musik 34 Videos 125 Провожаем осень с плейлистом от Вити. Как зайти без тора: Через. Разное/Интересное Разное/Интересное checker5oepkabqu. Предложение от конкурентов под названием hola! Onion - Нарния клуб репрессированных на рампе юзеров. После всего проделанного система сайт попросит у вас ввести подтверждение на то, что вы не робот. Для того чтобы зайти в Даркнет через Browser, от пользователя требуется только две вещи: наличие установленного на компьютере или ноутбуке анонимного интернет-обозревателя. А ещё его можно купить за биткоины. Именно благодаря этому, благодаря доверию покупателей,а так же работе профессиональной администрации Меге, сайт всё время движется только вперёд! Имеет оценку репутации из 100. Нужно знать работает ли сайт. Если вы используете импланты MegaGen AnyOne, покупайте изделия, совместимые с МегаГен. Onion/ - Psy Community UA украинская торговая площадка в виде форума, наблюдается активность, продажа и покупка веществ. Основателем форума являлся пользователь под псевдонимом Darkside. Mega darknet market Основная ссылка на сайт Мега (работает через Тор megadmeovbj6ahqw3reuqu5gbg4meixha2js2in3ukymwkwjqqib6tqd. Безусловно, главным фактором является то, что содержание сайта должно быть уникальными и интересным для пользователей, однако, Вы можете узнать что то новое из опыта других. Silk Road (http silkroadvb5piz3r.onion) - ещё одна крупная анонимная торговая площадка (ENG). Как зайти 2021. Telefon oder E-Mail Passwort Забирай! Onion - Stepla бесплатная помощь психолога онлайн. Ранее стало известно, что в Германии закрыли крупнейший онлайн-магазин наркотиков «Гидра». Присутствует доставка по миру и перечисленным странам. Скорость загрузки страниц. Zcashph5mxqjjby2.onion - Zcash сайтик криптовалютки, как bitcoin, но со своими причудами. Форум это отличный способ пообщаться с публикой сайта, здесь можно узнать что необходимо улучшить, что на сайте происходит не так, так же можно узнать кидал, можно оценить качество того или иного товара, форумчане могут сравнивать цены, делиться впечатлениями от обслуживания тем или иным магазином. "ДП" решил.